Evaporation technology
Vacuum evaporator, forced & natural circulation evaporator, thin film evaporator & falling
film evaporator for efficient process wastewater treatment and for process liquids
Evaporator plants are needed to process industrial process fluids. A vacuum evaporator separates liquid media and liquid mixtures to obtain clean solvents and to solve various separation tasks. This process takes place mainly under vacuum or atmospheric. The vacuum reduces the boiling point of the solvent. During evaporation, the low-boilers separate from the high-boilers. The recovered, clean solvent can in many cases be reused in your industrial process.
The medium to be separated is the concentrate. Due to the less complicated handling you only incur minimal disposal or further processing costs with a vacuum evaporator. For every requirement we offer most efficient and specially designed evaporator system and units with different performance and designs, forced- and natural circulation evaporator, falling film evaporator and thin film evaporator.
Vacuum evaporators are a frequently used equipment in chemical industry to purify or recover solvents. Our competent staff can advise you on the selection of an evaporator system to solve your tasks.
We gladly advise you on the selection of a best possible evaporator system for your task. We guarantee our partners and customers maximum safety and
first-class quality of our services and products. We are happy to take over the planning and execution of the new construction of industrial and chemical
installations and show you possible optimization potentials in older evaporator systems.
Falling film evaporator
Falling film evaporators for very gentle evaporation applications
Falling film evaporators are recommended for the use in the industries of pulp & paper, food processing, beverage, pharmaceutical and in the chemical industries. In this evaporator system, the liquid in the tube evaporates to an uninterrupted liquid film. Of importance is that the coherent falling liquid film does not break. The falling film evaporator systems that we offer are ideal in combination with vapor recompression systems. A minimal product-side pressure drop, heating surfaces >500m², a compact design, minimal operating volume, none to very low super heat, a short residence time and an excellent heat transfer characterize our falling film evaporator systems.
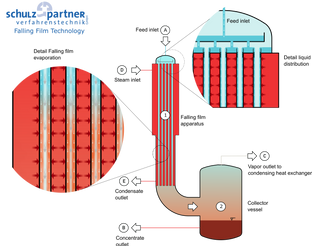
The most important features at a glance:
- excellent heat transfer
- short holding time
- no super heat on process media
- minimal operating content
- compact construction
- heating surfaces higher than 500 m²
- minimal pressure drop on product side
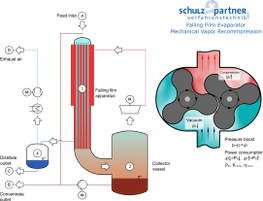
Falling film evaporators with mechanical vapour re-compression
Compressors of various types are used for mechanical vapour re-compression.
In addition to the commonly used axial fans, piston, screw, roots and axial compressors are used. Some types only need the heating steam to start up.
During operation, vaporisation energy is completely supplied via the compressor motor as an electric current.
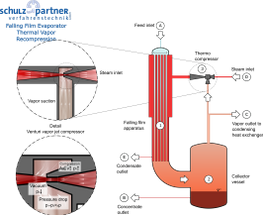
Falling film evaporator with thermal vapour re-compression
The vapours are compressed with the help of a Venturi steam jet compressor. The compressors are designed for constant operating conditions and their efficiency drops sharply in partial load operation.
- Simple construction without moving parts, therefore very robust and reliable
- Steam savings 30 to 50% depending on operating ratio
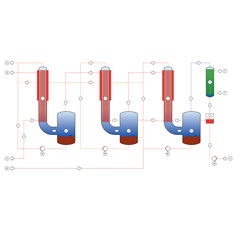
Multi-stage falling film evaporator
The evaporation of water comes with a very high specific energy consumption. This is significantly higher than that for the evaporation of solvents.
Multi-stage evaporators are one way to reduce this energy consumption; the vapours exiting the first evaporator are used to heat the second evaporator, the vapours from the second are used to heat the third and so on.
The system’s energy requirement thus decreases with each additional evaporator stage, however the investment costs are correspondingly higher.
System example FFVE
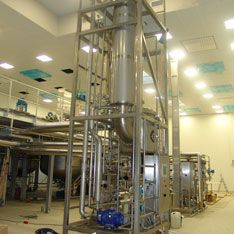
FFVE 300- hydroxyethyl starch concentration
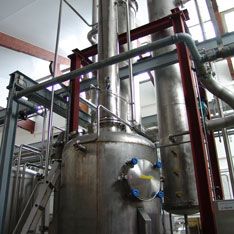
FFVE 1800- malt extract
CONCENTRATION
Natural circulation evaporator
The natural circulation evaporator does not require a hydraulic pump to circulate. The circulation is generated by natural convection by heating and boiling. This system is suitable for many tasks, among other systems for use for distillation with a rectification column. They are used at pressures of <50 mbar and higher. Except for the surface evaporation, the depth of the heat exchanger is a decisive factor. Natural circulation evaporators work to the following principle: The liquid lift that is caused by liquid expansion during heating, the liquid arises from the fact that the density of the heated liquid area in the natural circulation evaporator is lower than that of the colder liquid. The same happens after evaporation because the vapor are less dense than the liquid. This mechanism generates a circulation flow. This continuously circulates the fluid around the heat exchanger without the need to use an additional pump. You save operating and investment costs.
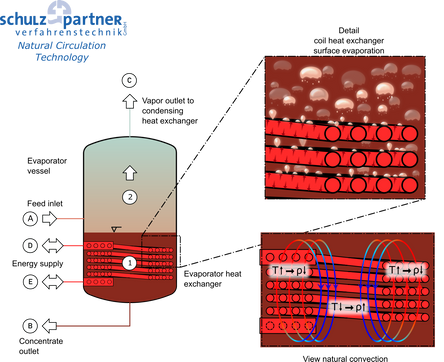
Thanks to its simple design, this evaporator is extremely robust and reliable.
It uses the thermo siphon principle and therefore generally works without a circulation pump. Only for liquids with difficult conditions, such as solids content, crystallization or increased viscosity, must successful circulation be supported with a pump; usually with a pipe arc propeller pump.
Typical applications:
- Evaporation of clean liquids with normal viscosity
- Sump evaporator for rectification columns
Natural circulation evaporators can alternatively be used in conjunction with a circulation pump as evaporation crystallisers.
Forced circulation evaporator
In addition to the natural circulation evaporator, we also offer the forced circulation evaporator.
The difference to the natural circulation evaporator:
The evaporation happens flashing the superheated medium in the flash-tank and not already in the heat exchanger tube.
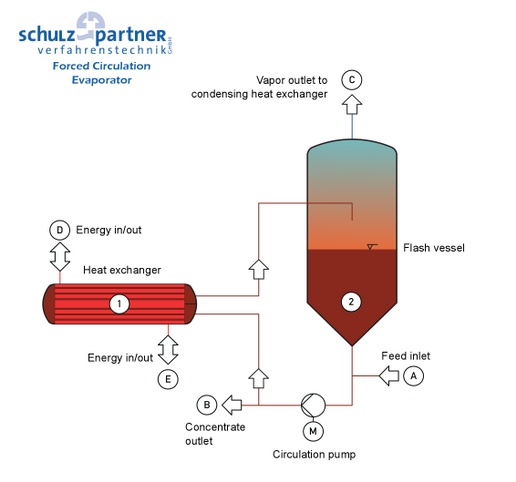
In contrast to natural circulation, the evaporation does not take place in the heat exchanger tube here, but only when it enters and flashes in the downstream separator. The product is circulated over the heat exchanger by a pump. The fluid on the product side is flowing with slight overpressure, for example by an orifice, so that the liquid flow is super heated only by a few degrees without evaporating.
Typical applications:
- Evaporation of soiled, crust-prone liquids
- Evaporation of viscous products
System example FCVE
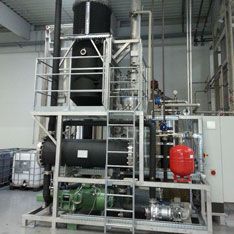
FCVE 100 - OIL DEHYDRATION
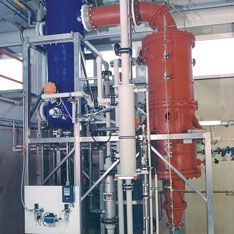
FCVE 140 S - Recovery of Sulfuric Acid
Thin-film evaporator
Thin Film Evaporator - for viscous to high viscous solutions
Our thin-film evaporators are specially designed to separate temperature-insensitive products by evaporation. Thin-film evaporators proceed thermally with a mechanically generated thin liquid film. From the rotating wiper, the flowing liquid medium is evenly distributed on the tube inner wall. This film has a thickness between 0.1 to 2 millimeters, depending on the viscosity of the product and contact pressure of the wiper. It ensures the shortest residence time and high evaporation rates. Our thin-film evaporators enable you to produce temperature-insensitive, high-quality products. We offer you evaporator systems for every task as a special as well as in a classic design.
Our thin-film evaporators are ideally suited for the following applications:
- Pure distillation of high boiler
- Treatment of high-viscosity media
- continuous drying processes
- Degassing or removal of volatile components from highly viscous media
Contact us, our friendly staff will take their time to give you detailed advice and answer your questions.
Heat pump evaporator
The evaporation of the solvent and the subsequent condensation take place in this process by using the hot or cold side of a refrigeration cycle (compressor, refrigerant). Apart from a power connection, the system requires no further energy, such as heating media or cooling water. The energy consumption (heating and cooling energy) is reduced to about 10% compared to a conventional single-stage evaporation.
We offer three different heat pump evaporators as standard systems:
- EVA natural circulation evaporator
- CONfix® forced circulation evaporator
- DRYfix® dryer
Custom-made products are of course also possible on request.
This type of system offers a number of positive features:
- 90 % energy saving
- no energy sources such as steam, hot water, etc. required (only one power supply is needed)
- no cooling water needed
- self-sufficient systems
- modular design
- prefabricated in the rack
- pre-tested systems
- low boiling temperature in a vacuum (<50°C)
Operation in a vacuum offers further advantages, such as reduced corrosion. It allows the use of heat-sensitive products and, when using of a plastic heat exchanger, the concentration of hydrochloric or hydrofluoric acid is also possible.
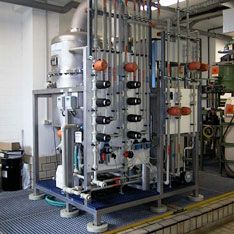
EVA - Natural circulation evaporator with heat pump
This type of system is particularly suitable for smaller quantities and simple tasks.
The medium is sucked into the concentration stage via negative pressure and heated there by means of a heat exchanger in which the refrigerant condenses. The medium is thus concentrated to a consistency that is still flowable. The resulting water vapour flows into the condensation stage and is condensed there upon evaporation of the refrigerant. The distillate is discharged through the vacuum system.
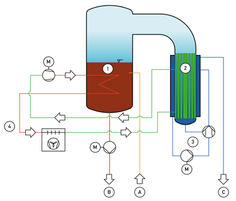
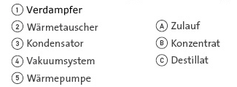
System example EVA
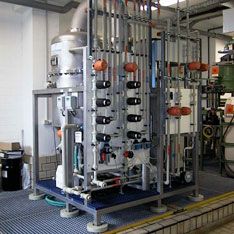
EVA 100 - Process waste reduction
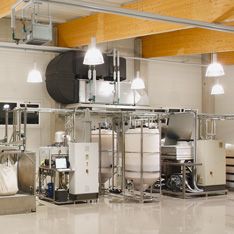
EVA 450 - Concentration of Thermal water
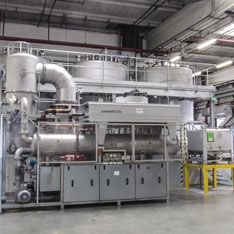
CONfix® - Forced circulation evaporator with heat pump
If a medium that tends to form deposits has to be concentrated, then this forced circulation evaporator is the right system. The medium is passed into the expander through a circulation pump via an external heat exchanger. The radiator only performs the warming; evaporation first takes place in the expander, whereby a deposit formation is strongly reduced.
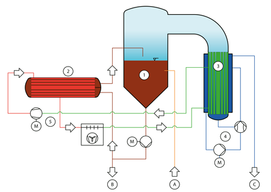
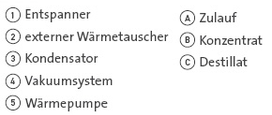
System example CONfix®
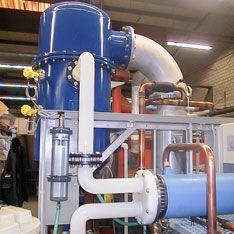
CONfix 190 - Chromic acid concentration
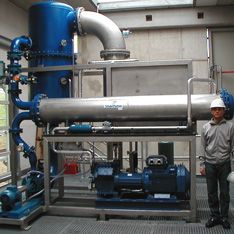
CONFIX 450 - Ethanol recovery Distillation unit