Schulz+Partner GmbH - Services
Feasibility studies, pilot projects, Basic-and Detail Engineering, plant design und service customer care
Schulz+Partner is your partner for thermal process engineering and the processing of process fluids. We not only offer optimisation options for existing systems and processes, but also provide all planning and development work for the construction of chemical and industrial installations.
-
Preliminary planning/ Feasibility studies
-
Laboratory tests and pilot plants
-
Basic- and Detail Engineering
-
Construction/ 3D Modelling/ technical communication
-
Service/ After-Sales-Service
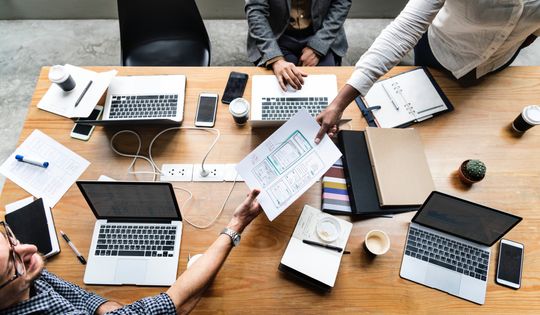
Feasibility studies
Feasibility studies are performance phases that we offer to our customers and partners. These are comprehensive studies and serve in detail to identify information of a project. It takes into account risks, points of view and conditions such as time frame, costs and quality.
The aim of a feasibility study is to determine whether the project will be continued, redesigned or completely given up.
Following points will be worked out in exchange with our customers:
- Determine the physical properties, chemical resistants materials and special requirements.
- Determining the physical and chemical feasibility
- Risk assesment
- Consideration of profitability and amortization
- Estimation of technological volume, space requirements and installation
- Visualization of the process or the process steps
- Determine the automation requirements and instrumentation and control structures
- Performance visualization for the entire project
- Design of energy and mass balances
- Design of the necessary peripheral systems
- Design of the room structures
- Selection of bringing in and installation options
- Cost estimation
Material und Media
The choice of materials always depends on the type of application. We select only high-quality and durable materials to guarantee high process reliability as
well as a long service life of our systems.
For example, we use:
- Stainless steel
- High-alloy stainless steels (1.4539, 1.4563, 1.4562, etc.)
- Hastelloy®
- Steel (coated)
- Titanium
Depending on the media, the tanks and heat exchangers are provided with rubber coatings, PFA, E-CTFE or Blue Amor coatings, or lined with PVDF, graphite or PTFE. Heat exchangers are used impregnated with graphite or silicon carbide amongst others.
Acids
- Hydrogen chloride HCl
- Chromic acid H2CrO4
- Hydrogen fluoride HF
- Nitric acid HNO3
- Sulphuric acid H2SO4
- Phosphoric acid H3PO4
- and many more
Polymers
- N-methylbutyrolactam NMP
- N-methylmorpholine N-oxide NMMNO
- Polyvinylpyrrolidone PVP
- and many more
Solvents
- Dichlorethan C2H4Cl2
- Ethanol C2H6O
- Isopropanol C3H8O
- Hexan C6H14
- Toluol C7H8
- Heptan C7H16
- and many more
Process- and plant optimization
We not only offer all planning and development work for the construction of new chemical and industrial installations, but also optimisation options for existing systems and processes. Older systems in particular have great energy saving potentials. Recognising these and optimising them is today more sensible than ever. Thanks to our technical laboratory and test laboratory in conjunction with suitable PC software such as ChemCAD and not least thanks to our wealth of experience, we can, for example, optimally convert your systems to operation with new media and at the same time demonstrate energy-efficient solutions.
We work with software such as
ProSim | primarily for process optimisation and design |
HTRI | for heat exchanger and apparatus design |
Siemens S7, TIA Portal | for programming and system control |
WinCC flexible | for visualising the system control |
Autodesk Inventor / Plant 3D | 3-dimensional construction and drawings |
AutoCAD | 2-dimensional drawing and planning |
Axavia | Configuration software |
and various others...
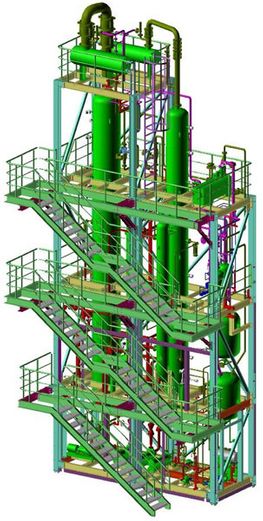
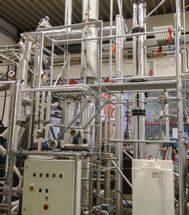
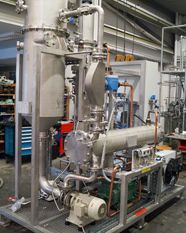
In addition to the feasibility study
For our customers and partners, we offer customized solutions.
For research or upscaling, it is often necessary to carry out feasibility tests on a laboratory or pilot plant scale.
For special analyzes, we include appropriate laboratories.
The experiments can be designed in different variants and together with the customer.
Our pilot plants
- Falling film evaporator 0.2 m²
- Thin-film evaporator dryer 0.2 m²
- Forced circulation/heat pump evaporator
- Crystallizer
- Rotary evaporator
- Rectification evaporator components: Gauze packing, slotted bottoms
- Extraction columns (Ø100/Ø150)
- Mixer settler
... are also available to rent upon consultation
Development and innovation
Process simulation, supplemented by pilot tests in our laboratory and pilot plant, forms the basis for a safe and optimal design of our plants.
The constant development and innovation of new technologies continue to ensure the fulfillment of the high demands of our customers in terms of economic efficiency and operational reliability of our products.
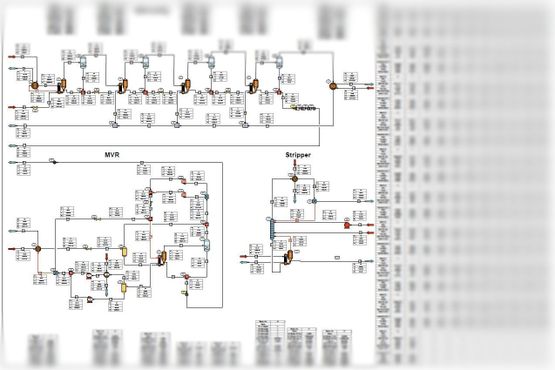
Basic Engineering
The design is based on the objective of a project. It leads to a work status of the documentation, with which the system to be designed is sufficiently defined for the actual execution.
The definition must be sufficient to describe performances qualitatively, to calculate costs incurred, to inquire services from subcontractors and to prepare appropriate official documents.
When planning the design, all parties involved in the project are informed comprehensively at the kick-off meetings about the state of planning, in order to ensure a smooth process. At these meetings, it is important to us to avoid misunderstandings and plan together in a structured way.
For these reasons, we give importance to a structured approach:
- The level of planning, e.g.
→ Thermal process
→ Peripherals
→ Scope of complete project
- The form of execution
→ Topic
→ Suggestions
→ Technical discussion and result. - Definition of tasks and their responsibilities.
Detail Engineering
Continuing and deepening the design is the Detail Engineering. This is to provide all documents for installation, operation, commissioning and service.
To start the execution, the following criteria apply:
- Basic engineering in sufficient quality
- Approvals of involved authorities
- Agreement of customers management
- Completed and clear revisions of the finalized draft
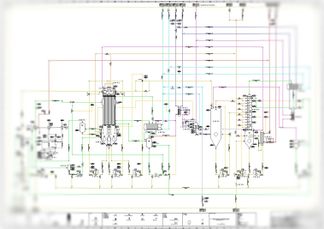
The timing and organization of the detail engineering depends on the overall scope of the project.
We define the conditions for the temporal coordination as important milestones.
We perform the duties in following order:
- Technical implementation of conditions and knowledge
- Receipt of final specifications / performance lists of the customer
- Match the entire planning
- Selection of subcontractors
- Plan, classify and design pipeline lists, supply and disposal networks
- Inquiry and quotation phase
- Plant design and controlling manufacturing plans
- Overall planning of the installation
- Finalization of execution documentation
- Planning control as a continuous action and
revisions on-site in case of deviations
We make our designs within a customers assignment as a part of a project. Due to increasing expertise and quality, we are gaining approval from our partners.
We gain customers to assist in the planning stages or the design process, its documentation
incl. the complete manufacturing process. This makes the construction in cooperation with the engineering one of our service pillars.
With Autodesk Inventor, Plant 3D and our know-how, we are able to represent and handle the complete technical communication with good quality.
3D models of apparatus'. Planned with a high degree of know-how and innovation
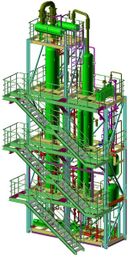
3D innstallation models including the complete design and calculations as well as piping planning, stress calculation, statics and more.
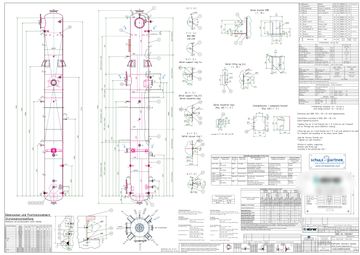
2D drawings of apparatus' and also layout design
We ensure our service for the sustainable quality of the supplied process plants. The service can be used throughout the lifetime of a system and provides professional support to our customers. The after-sales service and customer care offers a high value and is characterized by:
- High degree of customer orientation
- Quick responsing times in both, phone support and at site trouble shooting
- Distinct problem analysis with a high degree of detailing
- Their qualifications and many years of experience in addition SCC trained
- All-in-one knowledge that brings cost and time savings:
- Thermal Process Engineering
- Refrigeration technology acc. Regulation (EU) No 517-2014
- Electrical engineering acc. the latest VDE regulations
- S7 programming / visualization
- Assembly / installation
- Quick solutions
- Professional advisory
Our After-Sales-Service offers:
- Preventive maintenance
- Problem solving based on process engineering experience
- Performance solutions
- Spare parts service
- Qualified maintenance of refrigeration systems
- Remote maintenance via VPN / SINEMA RC
- Program updates and process optimizations
- Parameter analysis
- Upgrading of existing systems to another system or product
- Incorporation and training of operating personnel
Installations and supervision
In-house electricians and assembly staff manage and execute the final assembly.
Our specialists have many years of experience, qualifications and SCC training. They offer customers, a high level of safety.
Qualifications for special requirements are available, for example, installations in hazardous area or qualifications as a health and safety coordinator according to construction site regulations.
The advantage that we have, is the cooperation and the intensive information exchange of experiences with our planners. This concept allows our staff to perform the installation, assembly and the connections safely and smoothly.
Automation, HMI Visualization,
PCS-process support
The digital automation is for the operation of processes and process plants in factories, with minimal human intervention, and is nowadays indispensable.
We deliver process plants with their own control system. After commissioning, the programm will be provided to the customer.
However, it may happen that the systems control need to be implemented in an existing customer PCS (process control system) in the manner of the Industry 4.0 Evolution.
We support our customers in such processes and offer these as an independent service, including documentation and remote diagnostics together with their cooperation partners.
For the program we prefer SIEMENS Step 7, TIA Portal.
For HMI / displays we use ProTool, WinCC Flexible, InVisu.
In online remote diagnostics and online updates for the programs, we work with the classic VPN tunneling, the convenient and
safe SINEMA RC system from SIEMENS.
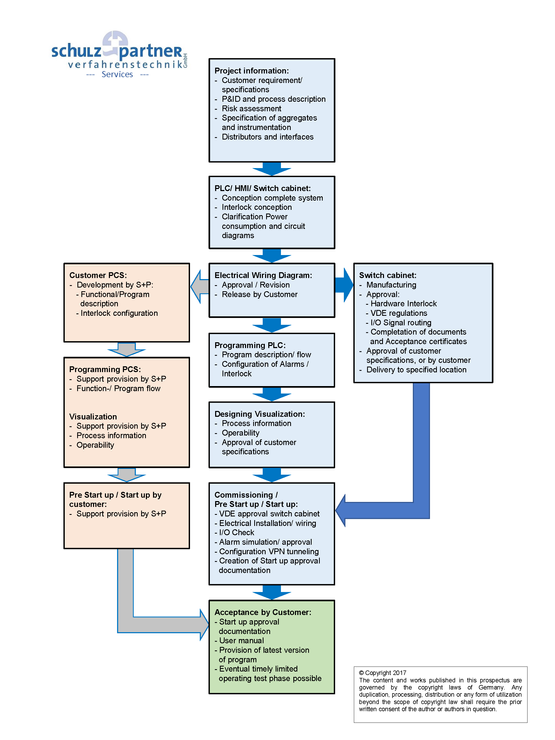
Pre-Commissioning
After the installation and assembly phase and before delivery, the mechanical and electrical installation will be pre-inspected by our skilled engineers and workers.
We perform the following aprovements and issue corresponding test certificates and protocols:
- Preliminary checks according to the latest VDE standards and regulations
- Electromechanical and mechanical safety devices
- Tightness control of systems and pipes under pressure
- Digital / analogue input and output testing of components within the skid
- Rotary field of motors up to opening and closing of automatic valves
- Simulation of alarms and their interlock, taking into account, even the visual visibility via the HMI.
- Individual functions of the modules and their interaction with eachother
- if necessary preliminary examination of the cleaning / CIP (cleaning in place) / SIP (sterilization in place) conception
- Parameter recording of operation with water or appropriate test media.
After the internal pre-acceptance, it is possible to carry out a
FAT (Factory Acceptance Test) with our customers.
Commissioning
Commissioning takes place at the end customer or operator at the planned installation site.
If pre-commissioning has been carried out, the connecting and connecting interfaces can now be checked and logged accordingly.
However, the following work is carried out before commissioning the product:
- Final acceptance test according to the latest VDE standards and regulations (if necessary by the customer)
- Re-testing of leaks of systems and piping under pressure and vacuum
- Digital / analogue input and output test of the remaining sub-installed components or perepherals
- remaining alarm simulation
- Rotation direction of motors
- Parameter and power consumption of operation with media provided by the customer.
After commissioning with product, and after the personnel briefing,
finally a SAT (Site Acceptance Test) can be carried out on site.
Training of personnel
Experience has shown that a process plant can only function as efficiently and trouble-free the plant operator or the maintenance personnel is taking care of it. It is often the case that in the event of a personal change or replacement of operators, the plant experience or know-how is not transferred. Due to not knowing how to handle the plant in certain situations, risks of accidents possibly even unexpected expenses and repair costs arise. This makes the training of operators and supervising specialists indispensable.
After each start-up, we assign the appropriate persons and groups. Even after a final acceptance, briefings and training can be done at any time.
The information will be provided as follows:
- Plant technology based on process diagram P&ID and live on the plant
- Explanation of the individual modules and their functions
- Corresponding guidelines and legal regulations
- Outgoing dangers and risks or explanations from the risk assessment of the plant
- Special features of the system
- Operation of the HMI and of the plant
- Functional sequence of the individual programs and subprograms
- Fixed set points and actual parameters that need to be checked and documented regularly
- User manual
- Classic cases of possible malfunctions and their corrections and explanation of their cause
- Recommended spare parts and recommendation of preventive actions
- Maintenance plan and regular inspections